Supply Chain Modernization: How to Align Your Approach with the Customer Experience
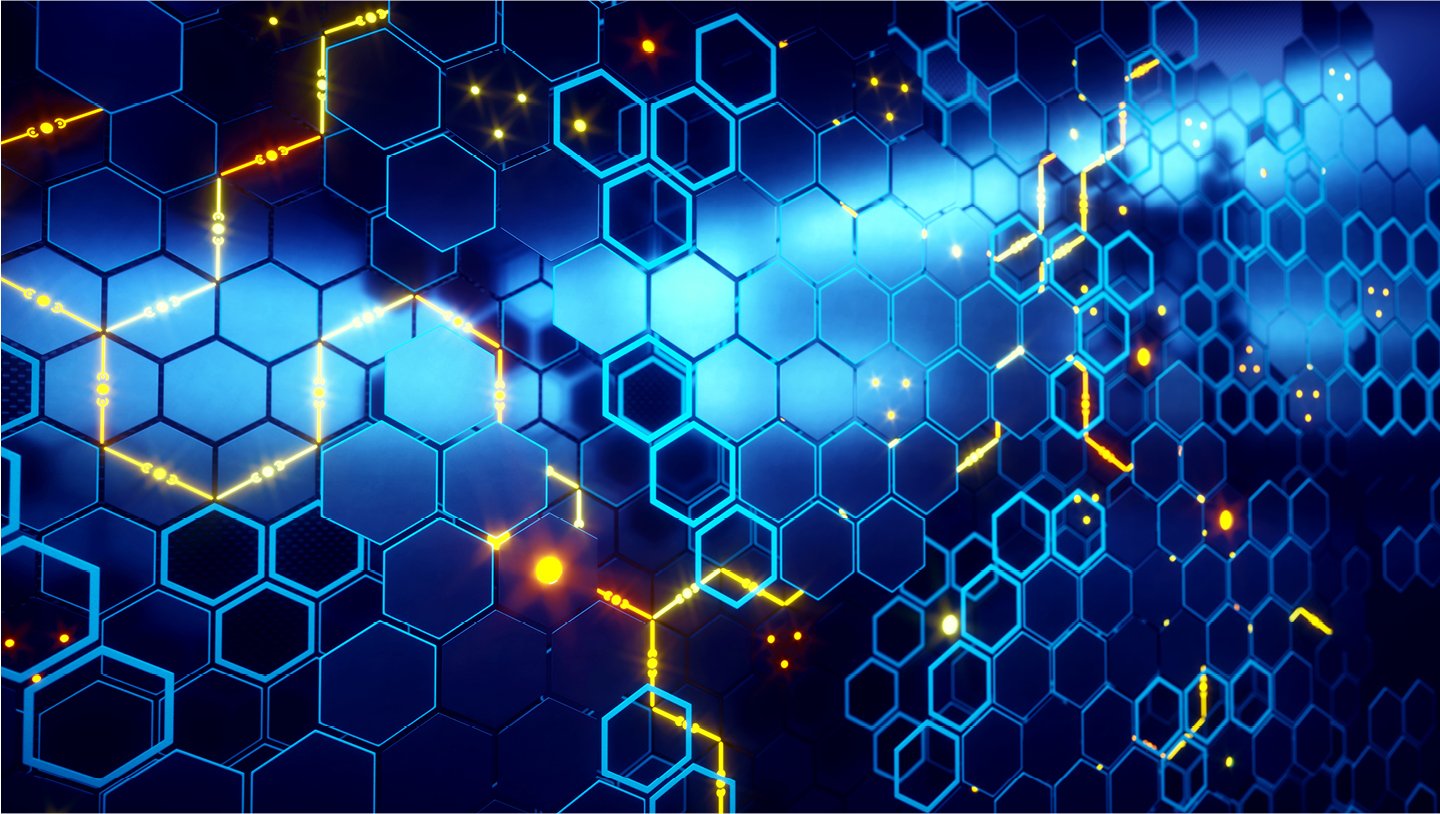
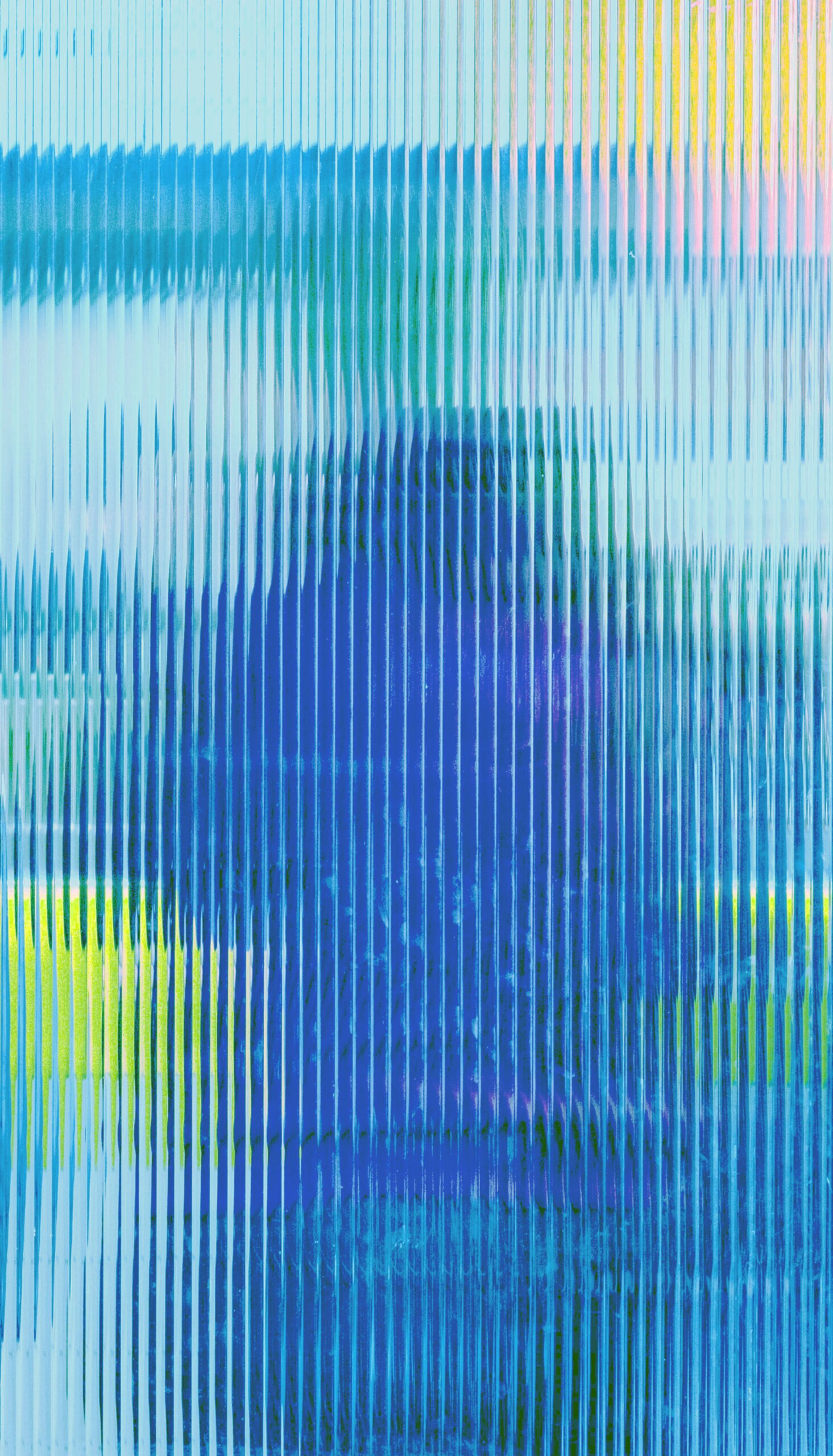
BRG is home to renowned thought leaders and experts considered authorities in their fields of work. Our timely research and perspectives provide analysis and insights on the most important issues facing the industries and organizations we serve.
Health First—Central Florida’s only fully integrated delivery network, operating four hospitals, and a multispecialty physician group—is pivoting to a consumer-centric culture with a primary focus on the customer experience. To deliver exceptional care in a dynamic environment, clinicians and support staff alike must have the necessary supplies. In practice, this involves supply rooms being appropriately stocked and easily navigable and assurance that supplies are safe for patient use. Supply Chain Operations (SCO) team members are critical for the care continuum, and well-executed inventory management processes benefit the patient.
Product availability throughout the supply chain continues to be a challenge post-pandemic, which creates a burning platform for reviewing the traditional PAR (Periodic Automatic Replenishment) inventory method. Health First prioritized implementing innovative ways to better manage and optimize its inventory processes and align with the customer experience.
The typical approach to inventory management involves a supply staff member (or inventory technician) scanning and counting nursing supplies with a handheld device or documenting with a clipboard and paper. The inventory tech notes supplies that need to be replenished, or “brought up to PAR,” and then refills the bins on another trip, usually within the same day. However, this method is usually assessed and replenished based on the experience of the inventory tech, or “gut feel,” which leads to counting all supplies and overstock. Additionally, this process leads to product expirations and inability to manage the PARs. This can lead to stockouts, where someone will notify the material management department to have them make an accelerated delivery of the supplies (a “demand call”), or nursing staff will search and pull supplies from another location.
Health First determined that it needed to deploy a new, innovative approach to manage supplies due to the amount of excess inventory, expired products, and lack of process and communication. Berkeley Research Group (BRG) professionals, along with the Health First SCO team, developed a program known as the Supply Chain Modernization Initiative, focusing on refining the organizational structure, rewriting job descriptions, developing standard operating procedures, establishing and measuring key performance indicators (KPIs), and deploying analytical tools that provide inventory insights.
Most important, the program involved implementation of a Lean Manufacturing approach (Two-Bin Kanban and 7S) to develop and maintain an efficient process and workplace. The Two-Bin Kanban (2BK) System process eliminates or reduces waste and focuses on the timely replenishment of supplies and creating an effective way of maintaining enough stock of high-consumption items near patient care areas. This approach blends process benefits and analytical measures to improve product availability and optimize inventory management practices. The 7S (Sort, Set in order, Shine, Standardize, Sustain, Spirit, Safety) approach creates a disciplined process with the staff to organize and maintain a safe, clean, and productive workplace while reducing waste and improving efficiency and quality.
Related Professionals
Related Services
Related Industries
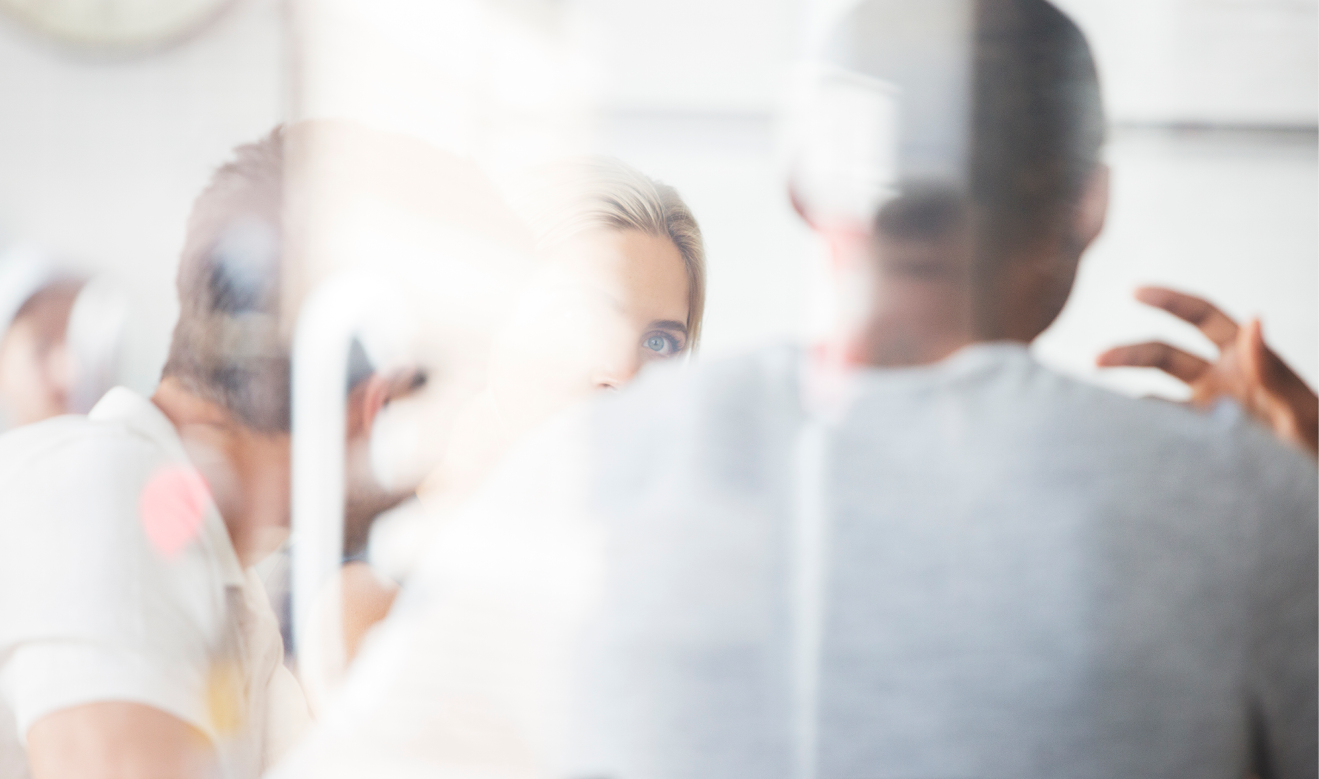
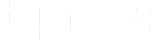
Prepare for what's next.
ThinkSet magazine, a BRG publication, provides nuanced, multifaceted thinking and expert guidance that help today’s business leaders adopt a more strategic, long-term mindset to prepare for what’s next.